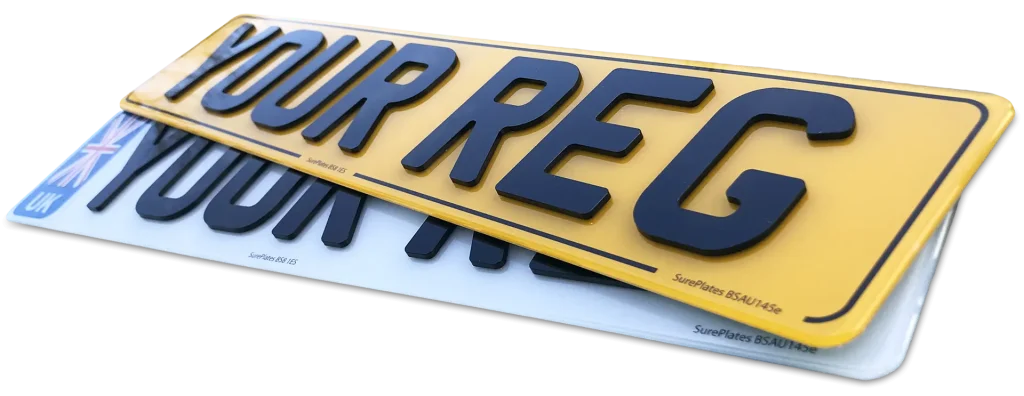
4D number plates have been steadily gaining popularity, and as we move through 2023, their demand shows no signs of slowing down. These premium number plates have become a go-to choice for car enthusiasts looking to add a touch of flair and style to their vehicles. They offer an easy and cost-effective way to personalise your car.
But have you ever wondered how these stylish and durable number plates are made? As part of our comprehensive series on road legal 4D number plates, we’re taking a dive into how they’re constructed. Every step in the manufacturing pipeline is carefully executed, ensuring consistent and reliable production processes and a high-quality final product.
Choosing the Perfect Material for Your 4D Number Plates
The production of number plates is a simple process that requires the use of a variety of materials and techniques, depending on the requirement. The selection of materials and techniques directly influences the quality, durability, and aesthetic appeal of the final product.
Materials
Among the materials used in number plate production, ABS plastic, aluminium, and acrylic are the most common. Each of these materials has its unique properties that make it suitable for specific applications.
ABS plastic
ABS plastic is known for its strength, toughness, and resistance to physical impacts. This makes it an excellent choice for creating durable and long-lasting number plates. It’s a cheap plastic, is easy to work with and can be cut by hand or by a CNC cutter. ABS cannot be laser cut, which is one downside.
Aluminium
Aluminium is lightweight and sturdy. It’s resistant to corrosion, which makes it a good choice for use outdoors. Aluminium number plates are often seen as a premium option due to their sleek, metallic finish. A downside is they are bendable and once bent, a permanent crease will appear. Shipping is more expensive as sturdier packaging is needed to prevent bending in transit.
Acrylic
Acrylic is the most popular choice by suppliers due to its versatility. It’s very easy to work with, is highly durable and long-lasting, and can be moulded or extruded into sheets of various thicknesses and then cut into various shapes and sizes. Acrylic can be cut by hand, or by automated CNC machinery like laser cutters or routers. Acrylic can be cut using a laser cutter, making it a great choice of material.
The most common technique used in number plate production is the 2-part method with acrylic. This involves using an acrylic blank that is laminated with an adhesive on one side. The adhesive side is then bonded to a reflective backing film. A printed number plate will have your registration pre-printed onto this film prior to lamination, whereas a 4D plate will not.
Crafting the Perfect 4D Characters: A Peek into the Process
The manufacturing process of 4D characters is very simple and reliable. At SurePlates, we take pride in crafting our 4D characters in-house, ensuring the highest quality and consistency.
The process begins with the proper selection of material. We use 3 mm and 5 mm black acrylic sheets for our 4D characters, but other materials can be used – aluminium is one such example. Acrylic is a highly versatile material known for its durability and excellent finish. It’s also easy to work with, has a great edge once laser cut, making it an ideal choice for creating the raised characters that give 4D number plates their distinctive look.
We work with acrylic in pallet loads. Acrylic sheets are laminated on one side with a high-strength adhesive to ensure proper application. A heated roll laminator is used to achieve this.
After lamination, the sheets are ready for cutting. We load them onto our laser cutter bed which is programmed with pre-made cut files for each character. The laser cutter is a crucial tool in our workshop as it allows us to achieve the precision and consistency required for 4D digits.
Each character takes approximately 25 seconds to cut. However, a high speed doesn’t compromise quality. Each cut is very precise – an accuracy of about 1/10th of a millimetre is typical for a modern laser cutter. This means every time the cutting head moves, it positions itself with a tolerance of about 1/10th of a millimetre.
After cutting, the characters are flipped over in-place and cleaned to remove the build up of black smoke that inevitably coats the backs of the digits. They are then given a quick visual inspection, are unloaded into alphabetised containers, and stored for use.
Precision is Paramount: The Process of Assembling Your 4D Plates
Now that we have the main component – the 4D characters – it’s possible to assemble your number plates. The first thing we do is print a work order document. This contains all your order information and some vital parts of the production process.
Print & Laminate Your Plates
One of our operatives will scan the barcode on your work order to initiate a print job. This print job is one of the automated processes in our production room. A print file is automatically generated using software and sent to one of several printers, depending on the printing needs. The print is put down on a piece of reflective backing film.
This film is then laminated to an acrylic blank, put through a compression roller, and any excess is trimmed off using a craft knife.
4D Jigs: Aligning Your Characters
Now we have your plates printed and laminated, it’s time to bond the characters to the plates. In case you didn’t know, the spacing and alignment of your characters is regulated by law. To ensure reliable and accurate application of your digits, we use jigs to accurately align them.
Your plate is placed inside a placeholder – a blank cutout in the shape of a plate that holds it securely in place. It can’t move once inside.
Number plate characters must be 79 mm tall and 50 mm wide, with an 11 mm gap in between. The two groups of characters must have a 33 mm gap between them.
With this information, we can make an accurate “placement jig” that matches these figures exactly. We have several dozen pre-made placement jigs on a rack for the various combinations of number plates we encounter.
We put the placement jig on top of the placeholder plate and secure in place with alignment pins.
So, now we have your plate secured in place with a placement jig on top that has holes cut out precisely matching the positions of your digits. Now all we do is pop the digits in the holes (adhesive side down, of course) and we have a finished plate.
Quality Above All: Ensuring Your 4D Plates Pass the Test
At this point, your number plates are completed and ready to be packaged. But before we despatch them, they need a quality check to make sure your plates meet a minimum quality standard.
The quality check involves the following points:
- Proof-reading the registration number.
- Checking for scratches, bubbles, marks, and dirt that may have gotten in while laminating your plates.
- Checking the size of your plates is correct.
- Checking the flag is correct.
- Checking the border colour, thickness, and radius is correct.
- Checking the markings are in the proper positions and are the correct colour.
For 4D and gel plates, we press the characters down using a hand-operated press set to a specific pressure. The adhesive is pressure-sensitive, so it needs a little pressure to fully activate and bond. The adhesive will continue curing over about 24-hours before fully setting.
Many suppliers neglect this part of the process, leading to premature failure of the plates and characters falling off.
Once the operative is fully satisfied that there are no imperfections or quality issues, your plates are packaged.
From Workshop to Doorstep: Packaging Your 4D Plates
Last but not least, we need to package your plates securely and send them to you. The first thing we do is place them face-to-face so the characters are touching. They are securely taped together using a low tack tape (usually masking tape) to prevent them from moving.
We place them face-to-face to avoid the surfaces of the plates or digits from being scratched during the harsh bumps and tumbles in transit. Each character is also covered by a protective film, further preventing scratches from accidentally occurring during transit.
Your work order, plates, and free fixing kit are then placed into a plastic sleeve, heat-sealed, and placed into a padded envelope. A dispatch label is then affixed.
That’s it – you’ll be able to install your plates in 1-2 business days!
Summary
Creating 4D number plates is a meticulous process that involves careful selection of materials, precise cutting of characters, and accurate assembly to ensure they meet the expected standards.
The production of 4D characters is a simple process that involves laser cutting and cleaning for precision and consistency. The assembly of the number plates is done with utmost accuracy, using alignment jigs to ensure proper alignment and spacing of characters.
Quality checks are always performed to guarantee the plates meet the highest standards, checking for imperfections and ensuring we have not made any mistakes with your registration number or plate configuration (border, flags, etc).
Finally, the plates are securely packaged and ready to be delivered to your doorstep. This comprehensive process ensures that when you choose 4D number plates from SurePlates, you’re choosing a product that has been crafted with care, precision, and a commitment to quality.